Разработка
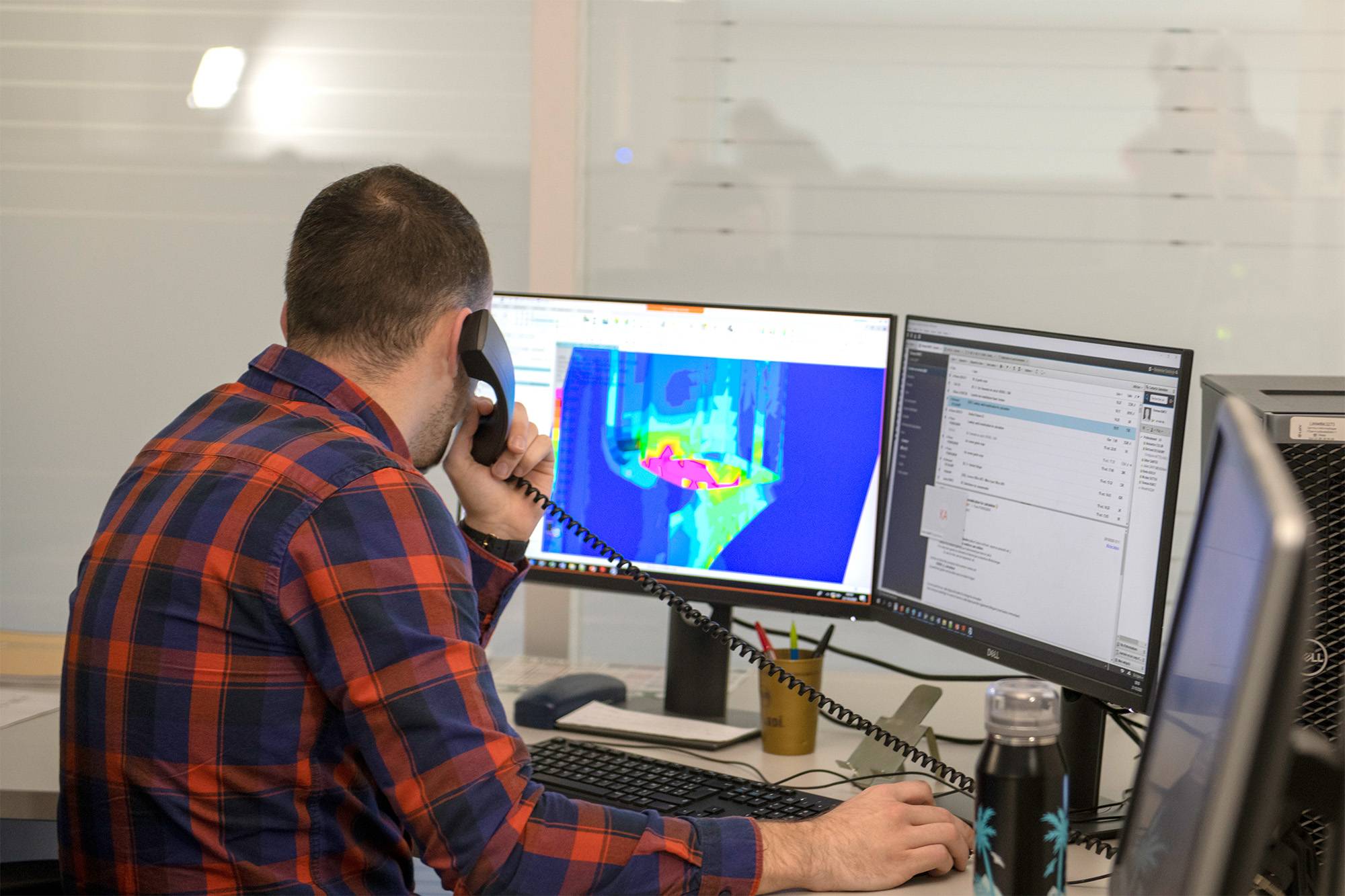
Группа Lohr развивает человеческие и технические ноу-хау и постоянно адаптирует их к новейшим технологиям.
Разработка решений предполагает оптимальное объединение ресурсов и компетенций в соответствии с принципами системной инженерии в области автомобильного и железнодорожного транспорта. Наши решения для автомобильной перевозки транспортных средств, а также для пассажирских перевозок и контрейлерных перевозок полуприцепов теперь действительно рассматриваются как самостоятельные системы, работающие в среде «систем систем».
Проектная площадка позволяет нашим специалистам согласовывать позиции относительно высказанных потребностей, разработки продукта, производственных мощностей, технического обслуживания и утилизации по окончании срока службы.
Будь то инновации, развитие или адаптация, главные участники процесса разработки:
Технический отдел:
- Он проектирует и разрабатывает каждый продукт, обеспечивает его ремонтопригодность и составляет соответствующую документацию.
- Он учитывает производственные мощности уже на этапе разработки.
- Для утверждения производственных и технических решений он осуществляет разработку, мониторинг и внедрение опытных образцов, а также головных серий.
- Он сравнивает результаты отдела расчетов с измерениями, проведенными во время динамических испытаний.
Отдел расчетов и моделирования:
- Он моделирует структуры конечных элементов.
- Путем моделирования он прогнозирует поведение конструкций, в частности усталость, динамическое поведение оборудования, а также тепловой, акустический и вибрационный комфорт.
- Он анализирует последствия изменений в определении продуктов после начала их промышленного производства.
- Он рассчитывает прочность конструкций с учетом профиля оборудования.
Тестирование
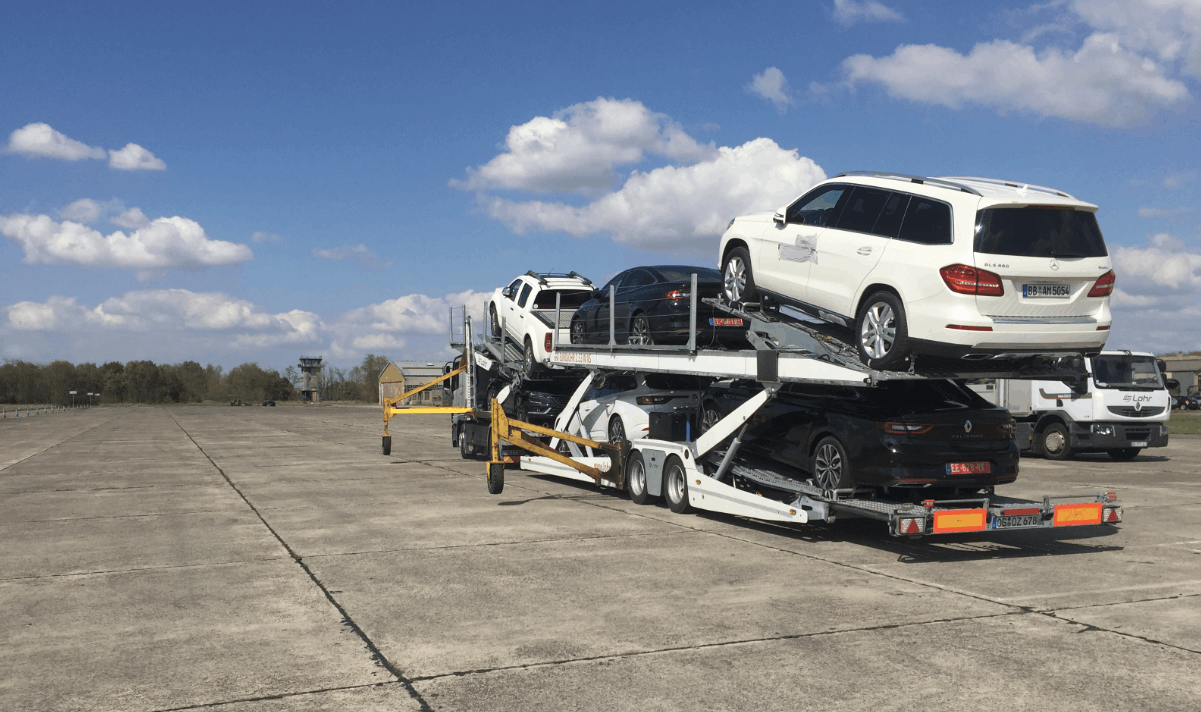
Испытания необходимы на этапах разработки и изготовления оборудования. Они позволяют гарантировать его долговечность и безопасность использования. С момента основания компании мы неизменно предъявляем высокие требования и проводим испытания подвижного состава, а также более или менее важных узлов.
Группа Lohr Industrie создала внутренний отдел для испытания автовозов, а также моделей Cristal и Modalohr. Самостоятельное проведение испытаний гарантирует оперативность и адаптацию на разных этапах разработки продукта:
- проверка оборудования и узлов на предмет соответствия действующим стандартам и директивам;
- проверка качества транспортных средств в целом или комплектующих от поставщиков в суровых условиях эксплуатации;
- помощь проектно-конструкторским бюро в вопросах разработки;
- объединение численных моделей расчета конструкций (корректировка значений нагрузок, рассчитанных по численной модели, с учетом реальных значений);
- экспертиза и определение источника дефекта, обнаруженного сервисным центром, в целях совершенствования процесса разработки.
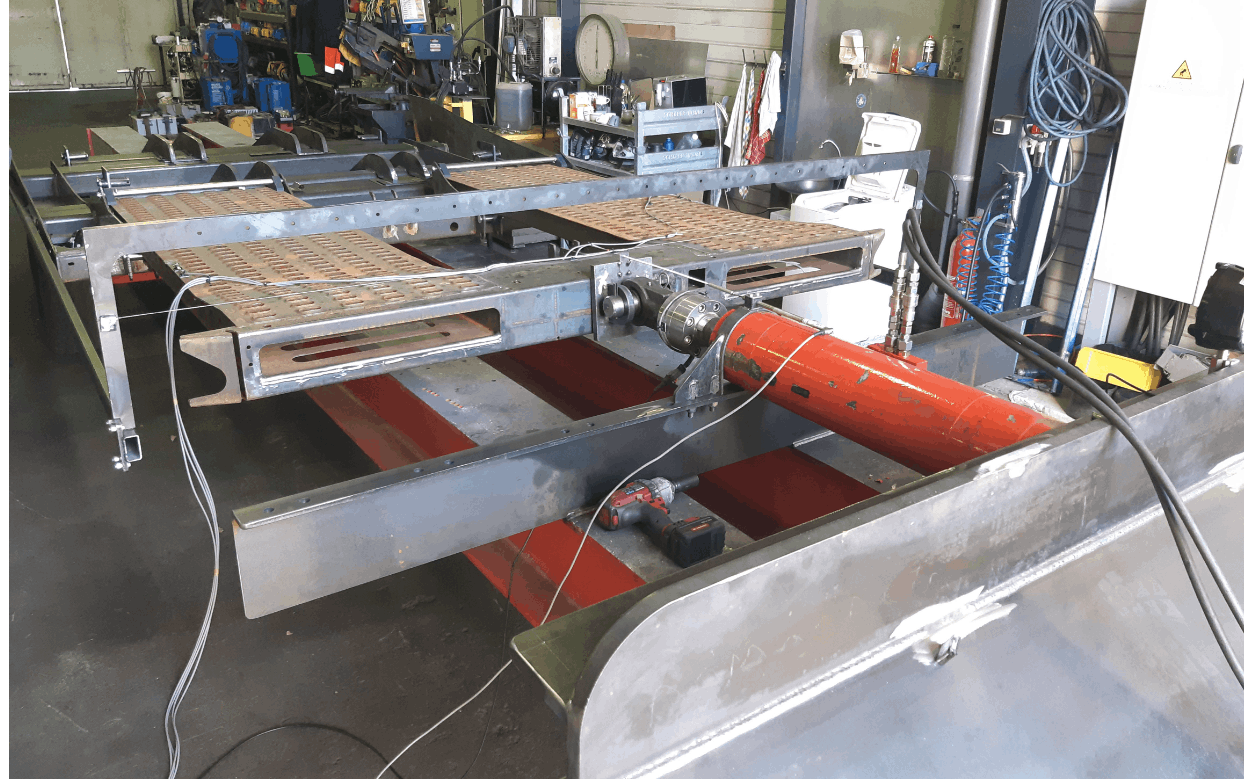
Мы можем проводить испытания с установкой на подвижном составе в условиях эксплуатации или испытания узлов в цеху, на стенде:
- динамическая езда подвижного состава в целом с контрольно-измерительными приборами (пример, езда автовоза на бывшей взлетно-посадочной полосе);
- приложение экстремальных нагрузок к подвижному составу в целом или к узлам (например, проверка прочности противоподкатного бруса сзади автовоза);
- механическая нагрузка для проверки усталостной прочности (несколько миллионов циклов) узлов на стенде (например, ходовая часть Cristal).
Мы располагаем всеми необходимыми средствами производства заводского типа для изготовления испытательных и специальных стендов:
- 3D-дизайн и 3D-моделирование;
- изготовление механосварных конструкций (резка, гибка, сварка, механическая обработка).
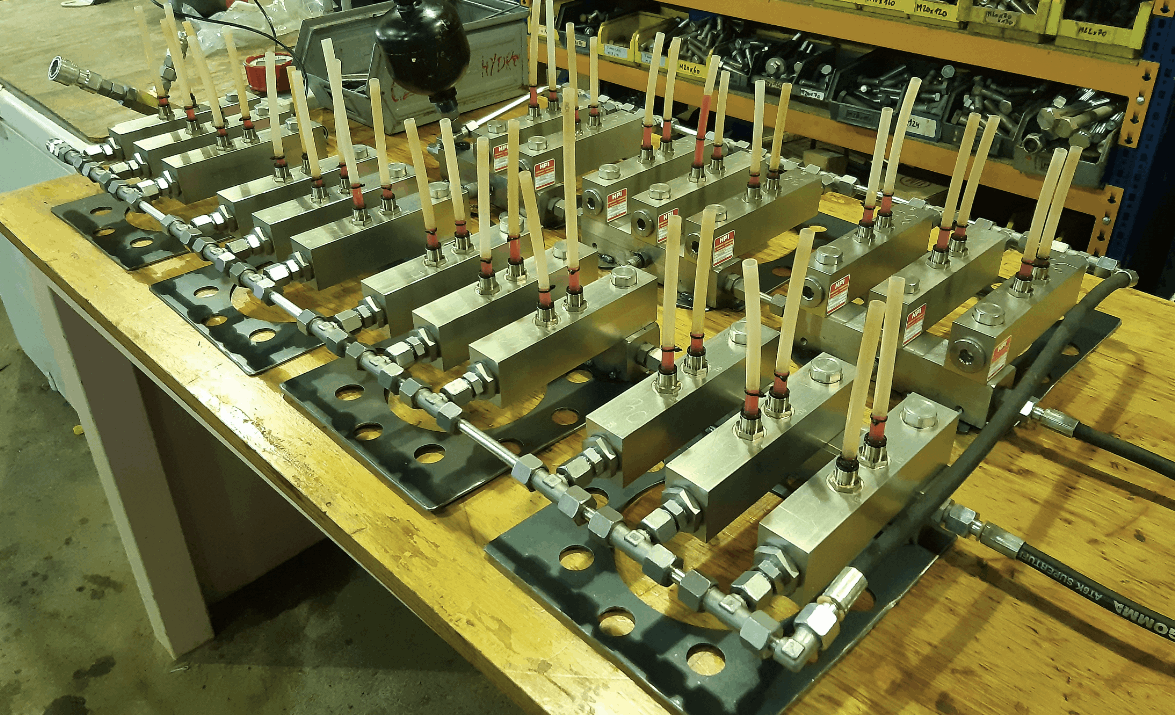
Мы используем широкий спектр контрольно-измерительных приборов, позволяющих измерять и фиксировать многие физические величины:
- гидравлическое и пневматическое давление;
- усилия;
- поверхностные нагрузки;
- перемещение, скорость, угол;
- ускорение;
- температура;
- напряжение, ток;
- звук.